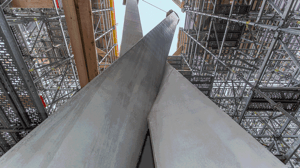
11m fair-faced concrete columns concreted from below
Headquarters Heidelberg Materials AG (Heidelberg, Germany)
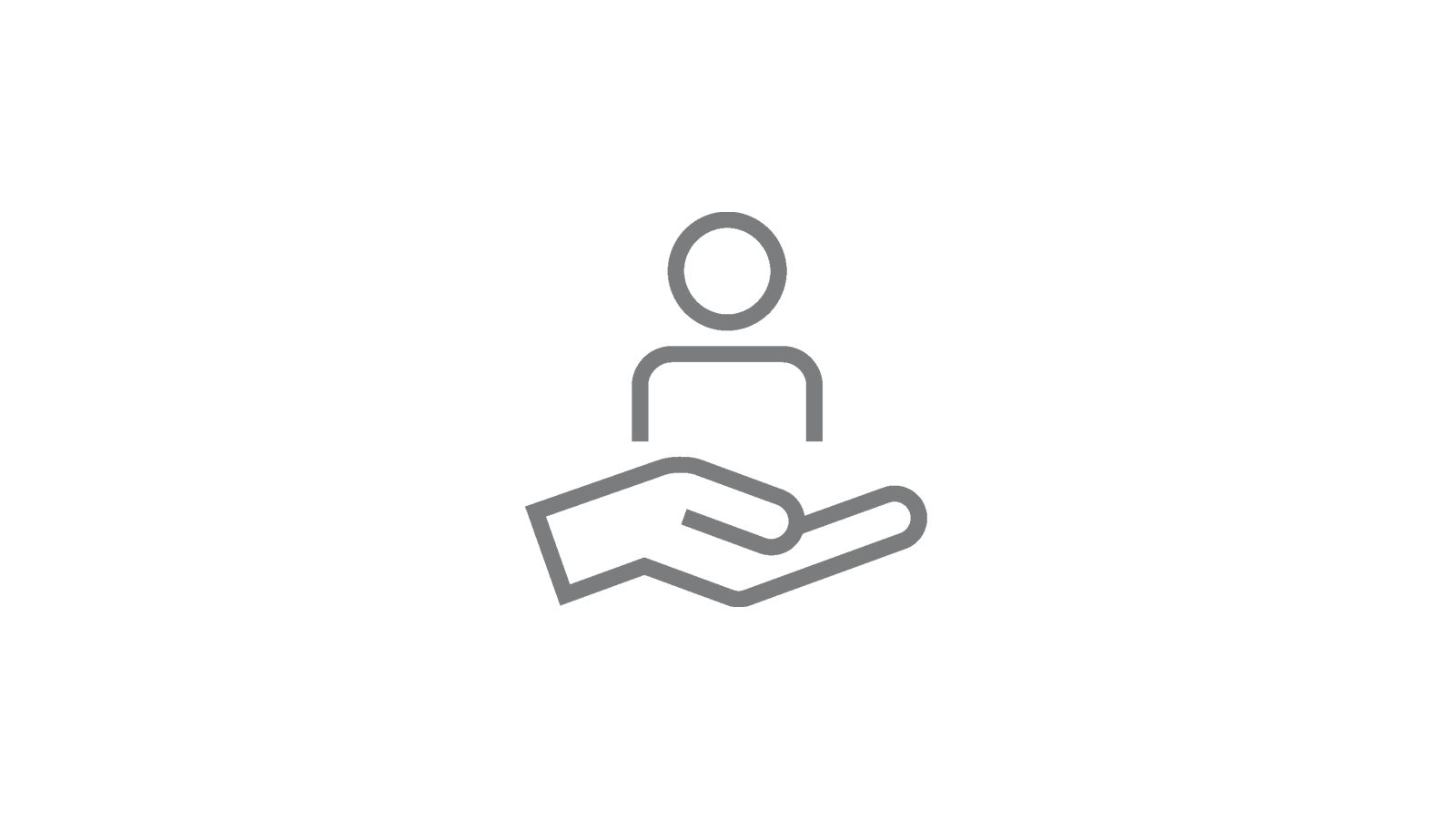
Diringer & Scheidel GmbH & Co. KG
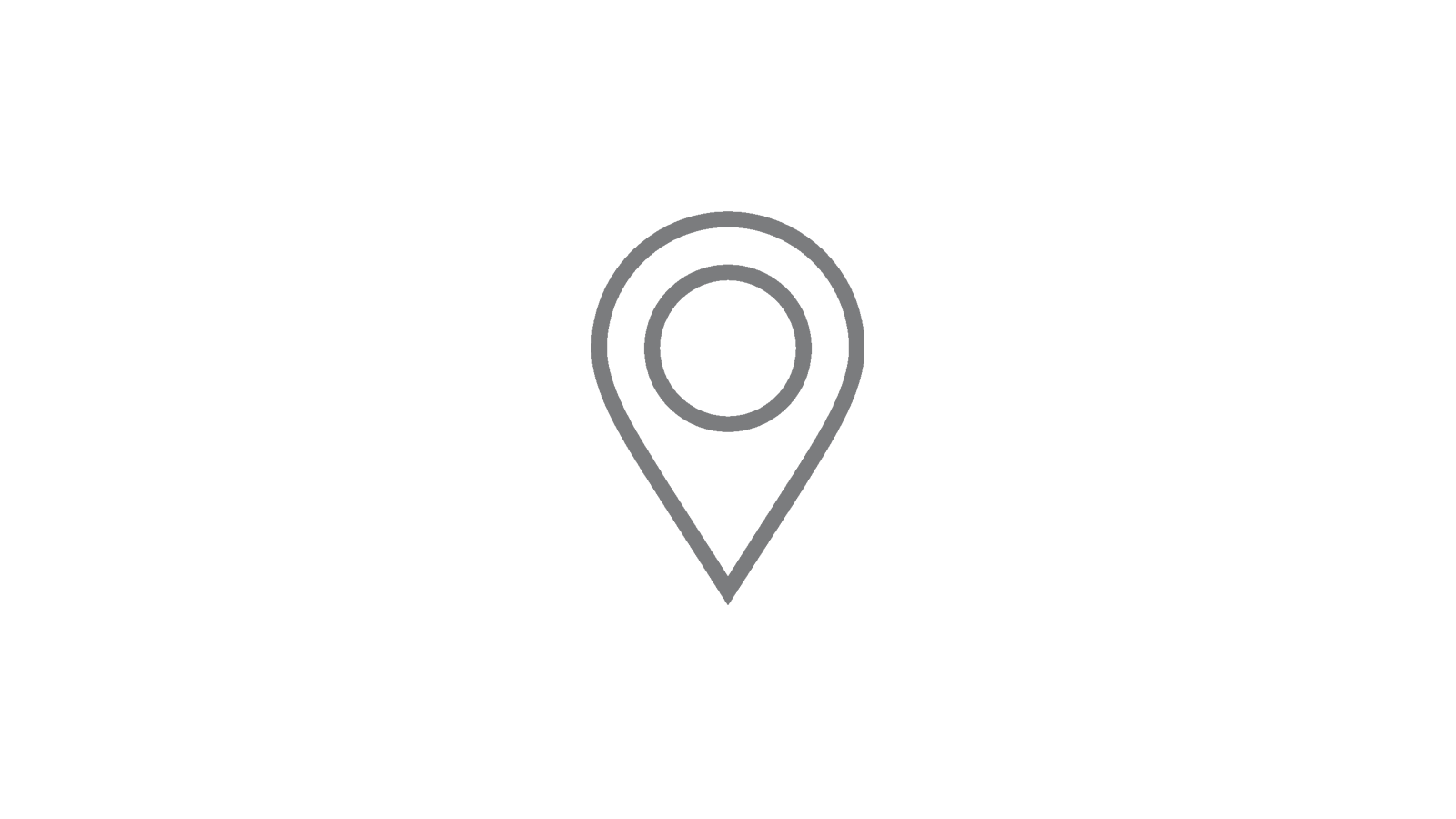
Heidelberg, Germany
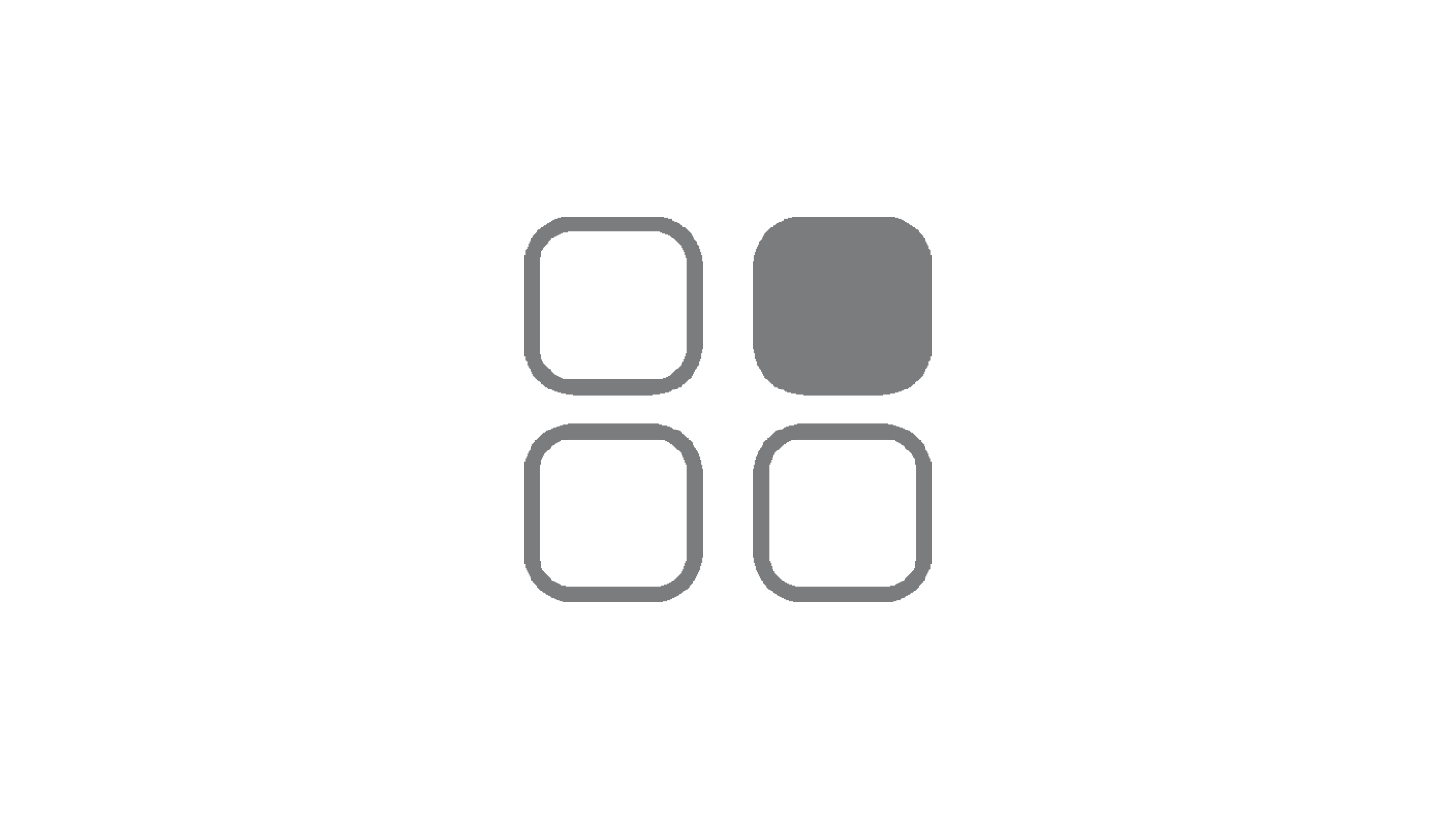
"Thanks to the pressure sensors from PERI, it was possible to solve this difficult task. We were not sure if it would be possible to pump the entire 30m³ of concrete from below."
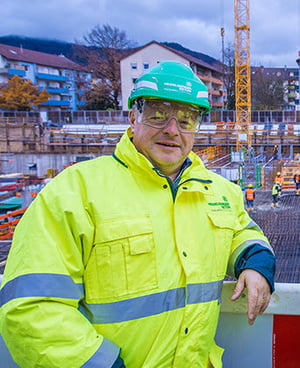
Headquarters Heidelberg Materials AG
Description
The new headquarters of the German building materials manufacturer Heidelberg Materials impressively demonstrates what is possible with concrete. In the highest exposed concrete quality of class SB 4 and using the finest white concrete, numerous architectural highlights can be found here. Spectacularly twisted tree supports, sweepingly patterned precast concrete facade elements and sharp-edged beams in a radiating pattern make the new headquarters based in Heidelberg a special eye-catcher. A total of 31,500 m³ of concrete was used to construct the building, which consists of three interconnected parts of different heights and was opened in June 2020.
Challenges
The center of the approximately 11 m high foyer of the Heidelberg Materials headquarters is formed by two groups of tree supports in SB 4 fair-faced concrete quality, which, from a structural point of view, serve as the root of the building. They each consist of three mutually inclined square cross-sections that intersect at approximately the lower third. The special feature: In accordance with the required fair-faced concrete quality, only a single element joint is visible over the entire column height of around 11 m. The element joints are of the highest quality. Beyond that, no fastening bolts, tensioning holes or formlining joints are visible.
For the realization of the tree supports, no special formwork made of wood came into question due to the very high architectural concrete requirements, the statically required fresh concrete pressure of 200 kN/m2 as well as the tight space conditions in the foyer. PERI therefore developed a highly complex 3D special formwork made of steel elements.
The supporting structure of the finished special column formwork was a sophisticated honeycomb structure consisting of 63 CNC laser-cut individual parts. These were assembled as a plug-in system in order to dispense with time-consuming welding. Each individual part had to be newly designed and statically dimensioned. A total of around 12.7 t of steel was used to produce this formwork. A 5 mm thick steel formwork skin was then applied to the supporting structure to withstand the high fresh concrete pressure. At the point where the arms of the three tree supports cross, additional external ring chord structures were installed to specifically counteract deformation of the steel.
Solution and results
Unlike usual, the tree supports were not concreted from above but from below. A concrete distribution system transported a total of 30 m3 of concrete simultaneously into three support sections and pressed the concrete upwards by up to 11.00 m via three pump hoses in the formwork.
Additional PREMO sensors integrated into the formwork made it possible to measure the fresh concrete pressure in real time during the concreting process and to monitor it via ISC web application on a cell phone.
The real-time data of the concrete pressure made it possible to adjust the concreting speed and make an informed decision to continue pumping from the bottom rather than filling from the top. This could have compromised the quality of the finished concrete surface.

- 11,75 m Fassadenstützen in SB 4 Sichtbetonqualität
aus Weißbeton
- individuelle Sonderschalungslösungen
- Unterstützung und Schulung des Baustellenpersonals bei der Umsetzung der komplexen Geometrien und Formen
- Termingerechte Materialbreitstellung und Koordination der Liefertermine
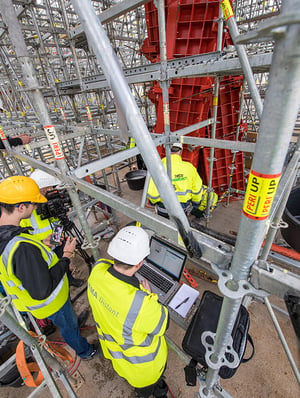
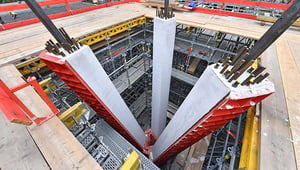

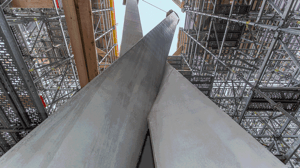
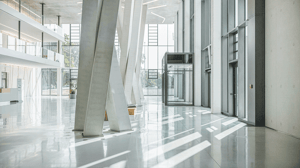
Curious?
We will present the solution to you in a 20-minute online demo without any obligation.